In the world of CNC (Computer Numerical Control) machining, plasma cutting stands as one of the most versatile and efficient methods for cutting metal. Whether you’re a hobbyist or a professional, understanding the intricacies of CNC plasma cutting can greatly enhance your work’s precision and efficiency. Among the various components that make up a CNC plasma cutting system, the PoKeys57CNCpro4x25 stands out as a powerful and essential tool for controlling the entire operation. This device integrates multiple functions and ensures smooth communication between the CNC controller and various peripherals, making it a must-have for advanced plasma cutting setups.
However, the PoKeys57CNCpro4x25 is just one part of the larger CNC plasma cutting puzzle. To achieve optimal performance, it’s crucial to have a reliable CNC controller with drivers, ensuring that all motors and axes move as they should, and that the entire system is synchronized. Furthermore, torch height control plays a vital role in maintaining the correct distance between the plasma cutter and the workpiece, preventing potential errors that can ruin the quality of cuts. Lastly, setting up the plasma cutter itself requires careful calibration, as improper setup can lead to inefficient cutting and unnecessary wear on the equipment.
In this article, we will explore each of these elements in detail. From the central role of the PoKeys57CNCpro4x25 in streamlining your CNC plasma cutting system to understanding the importance of torch height control and fine-tuning your plasma cutter setup, we will guide you through everything you need to know to optimize your CNC plasma cutting experience.
PoKeys57CNCpro4x25 – The Heart of Your CNC Plasma Cutting System
The PoKeys57CNCpro4x25 is a key player in modern CNC plasma cutting systems, acting as the central hub for controlling a wide range of functions. It is a powerful device that combines the functionality of a CNC controller with the precision of motion control, all within a compact and efficient package. Designed specifically for advanced machining applications, the PoKeys57CNCpro4x25 ensures that your plasma cutting system operates with unmatched accuracy and reliability.
At the core of the PoKeys57CNCpro4x25 is its ability to integrate seamlessly with other CNC components, making it a go-to solution for those looking to build or upgrade their CNC plasma cutting systems. Whether you’re setting up a new system or optimizing an existing one, this versatile controller offers features that make the entire process easier and more efficient. It can interface with a variety of devices, including motors, sensors, and external peripherals, ensuring smooth communication and data transfer across the system.
One of the standout features of the PoKeys57CNCpro4x25 is its robust I/O (input/output) capabilities. With a variety of input and output options, it provides excellent flexibility in controlling different elements of your plasma cutter. This includes controlling motors that drive the CNC machine’s axes, managing the inputs for limit switches and other sensors, and regulating the output for external devices such as a plasma torch. The ability to handle all these components within one controller drastically reduces the complexity of wiring and system setup.
For a CNC plasma cutting system, the precise control of motion is crucial, and the PoKeys57CNCpro4x25 excels in this area. With its advanced stepper motor control, it can drive multiple axes at once with smooth and accurate movements. This ensures that your plasma cutter operates efficiently, minimizing the chances of errors that could affect the quality of your cuts. Moreover, the controller’s real-time feedback system enables it to constantly monitor and adjust the machine’s movements, ensuring optimal performance during the entire cutting process.
Another significant advantage of the PoKeys57CNCpro4x25 is its compatibility with a variety of software platforms. Whether you’re using popular CNC machining software like Mach3, Mach4, or LinuxCNC, the PoKeys57CNCpro4x25 is designed to work seamlessly with them. This flexibility allows users to choose the software that best suits their needs while still taking full advantage of the advanced features and functions offered by the controller. Additionally, the device supports USB and Ethernet communication, providing fast and reliable data transfer for real-time operations.
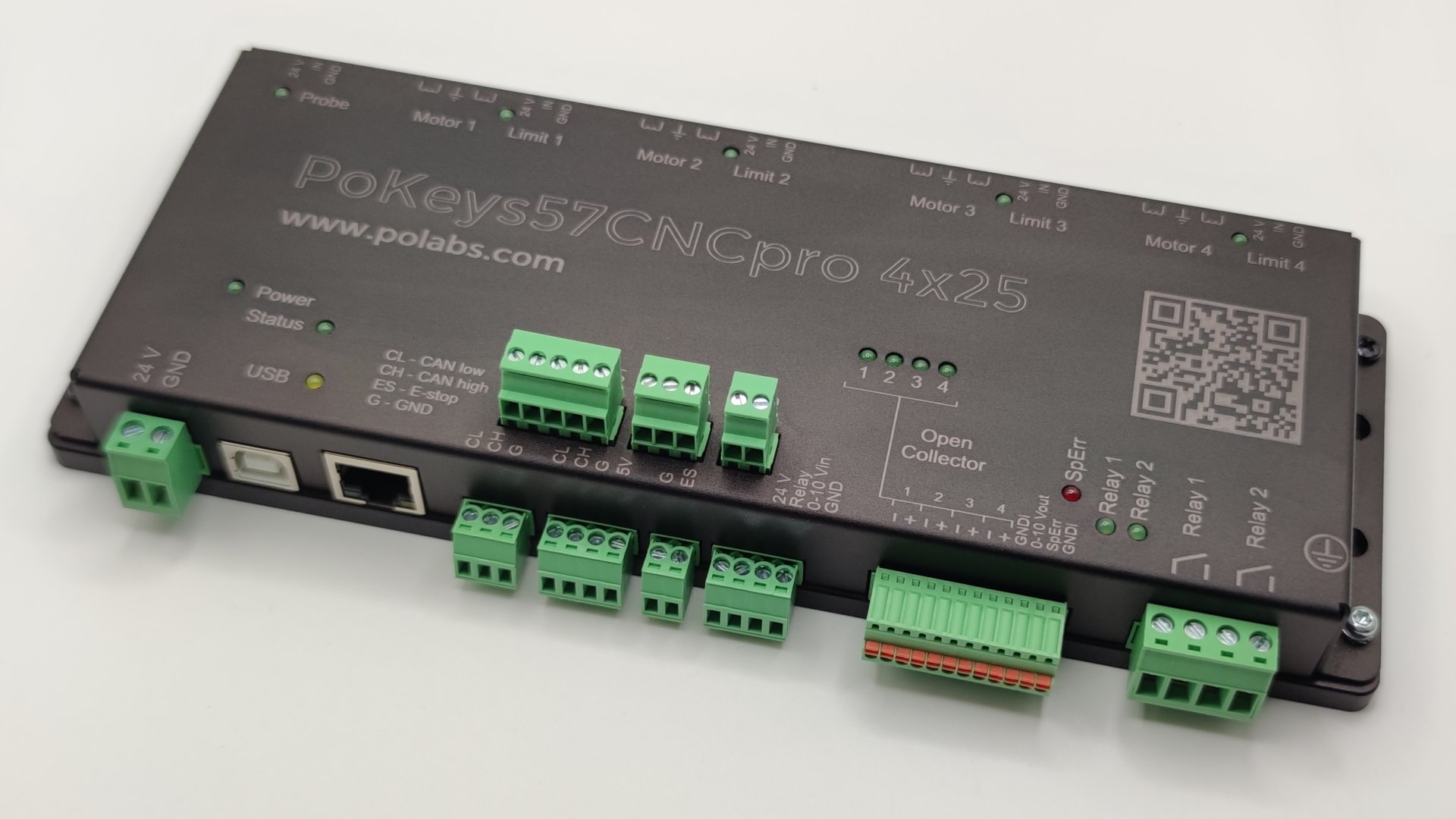
In the context of plasma cutting, the PoKeys57CNCpro4x25‘s versatility extends beyond just motion control. Its integration with a CNC controller with drivers and other critical peripherals enables you to fine-tune the performance of your entire system. For example, it can be used in conjunction with torch height control systems, which are essential for maintaining a consistent gap between the plasma cutter and the workpiece. With the PoKeys57CNCpro4x25 managing the communication and adjustments of these systems, you can ensure that your cuts are as precise and high-quality as possible.
In conclusion, the PoKeys57CNCpro4x25 serves as the heart of your CNC plasma cutting system. Its ability to control multiple components with precision, integrate with various software platforms, and provide real-time feedback makes it an indispensable tool for anyone serious about CNC plasma cutting. By streamlining the communication between the CNC controller, drivers, and peripherals, the PoKeys57CNCpro4x25 helps ensure that your system operates smoothly, delivering high-quality cuts with minimal errors. In the following chapters, we will explore the essential components that work alongside this controller to create a fully optimized CNC plasma cutting setup.
CNC Controller with Drivers – The Backbone of Precision in Plasma Cutting
A CNC controller with drivers is the essential framework that powers the movement of a CNC machine, and when paired with a reliable system like the PoKeys57CNCpro4x25, it becomes the backbone of your plasma cutting setup. The controller serves as the central brain of the operation, issuing commands to the drivers which, in turn, control the motors that move the machine’s axes. This synchronized movement is crucial for achieving precise cuts and optimal performance in CNC plasma cutting.
In a CNC plasma cutting system, the CNC controller with drivers ensures that the machine’s motors follow exact paths and speeds as dictated by the design or G-code file being processed. The PoKeys57CNCpro4x25 seamlessly integrates with these controllers, making it easier to manage and control the different components of the system. This includes controlling stepper motors or servo motors, which drive the x, y, and z axes of the cutting table. A properly configured controller ensures smooth, consistent motion, preventing errors like misalignment or jerky movements that could ruin the cut quality.
The role of drivers within the CNC system cannot be overstated. Drivers are the electronic components responsible for translating the controller’s signals into electrical current that powers the motors. These drivers play a critical role in ensuring the accuracy of motor movement by controlling factors such as torque, speed, and direction. Without high-quality drivers, the controller’s commands may not be executed precisely, resulting in erratic motion and errors in the cut. Therefore, choosing a reliable CNC controller with drivers is a crucial step in ensuring the system’s performance and longevity.
One of the key benefits of a CNC controller with drivers is its ability to control multiple motors simultaneously. In the case of a CNC plasma cutting system, this means the controller manages not only the linear movement of the cutting head (along the x and y axes) but also the vertical motion of the torch, which is critical for torch height control. Proper synchronization between these movements ensures that the plasma cutter maintains the right distance from the workpiece throughout the entire cutting process, preventing potential errors like excessive torch height or inconsistent cutting depth.
In addition to controlling motor movement, a high-quality CNC controller with drivers can also interface with additional sensors and accessories, further enhancing the system’s precision. For example, integrating limit switches and probes into the controller setup helps ensure that the plasma cutting system operates within safe parameters and avoids damage to the machine. Sensors can also detect changes in the material or tool, making adjustments to the system in real-time for even more precise results.
The PoKeys57CNCpro4x25 is particularly beneficial in this regard, as it facilitates communication between the controller and various peripherals, including torch height control systems. It’s common to see CNC controllers with drivers integrated into systems that use height control to adjust the position of the torch as it moves along the material. This dynamic control ensures that the torch remains at the ideal height, compensating for any variations in material thickness or surface irregularities that could affect the quality of the plasma cut.
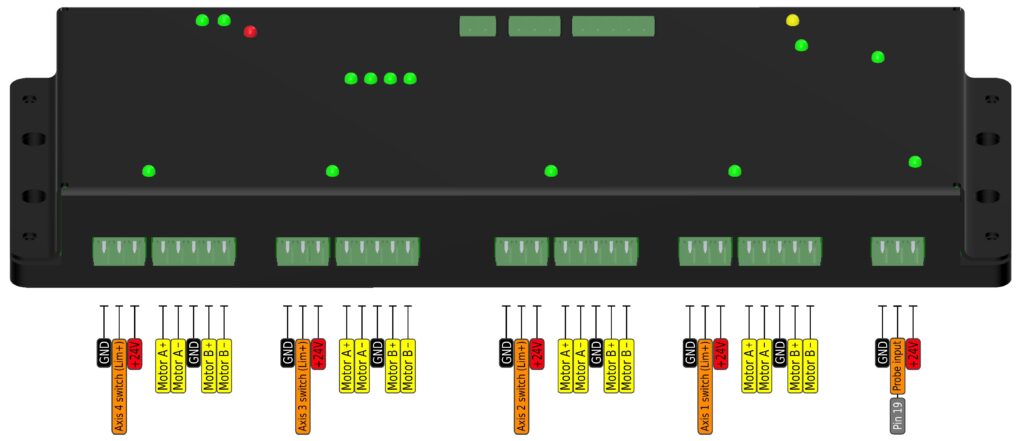
Choosing a CNC controller with drivers is not just about selecting a device that makes your machine move; it’s about ensuring that the machine moves smoothly, consistently, and precisely. The integration of the PoKeys57CNCpro4x25 with a well-designed CNC controller with drivers can elevate your CNC plasma cutting system to the next level. The improved motion control, real-time feedback, and compatibility with other components ensure that the cutting process is accurate, efficient, and of the highest quality.
In conclusion, the CNC controller with drivers plays a pivotal role in the overall success of a CNC plasma cutting operation. It allows for precise control over motor movement, synchronization, and the integration of various components such as torch height control and safety sensors. When paired with the PoKeys57CNCpro4x25, this system becomes even more powerful, providing a streamlined, efficient cutting experience that delivers consistent, high-quality results. As we move forward in this article, we’ll explore how integrating torch height control further enhances the precision of the cutting process, ensuring the best possible outcome in every plasma cutting job.
Torch Height Control – Ensuring Consistent Cuts and Optimal Performance
When it comes to CNC plasma cutting, one of the most crucial aspects of achieving high-quality cuts is maintaining the correct distance between the plasma torch and the workpiece. This is where torch height control (THC) becomes essential. The purpose of THC is to dynamically adjust the height of the plasma torch during the cutting process to ensure a consistent gap, optimizing the quality of the cut and prolonging the life of the torch and consumables. Without proper height control, the torch could be too close or too far from the material, leading to poor cut quality, excessive wear, or even damage to the equipment.
Torch height control is integrated into many modern CNC plasma cutting systems, and it works in conjunction with the PoKeys57CNCpro4x25 and the CNC controller with drivers to ensure the torch maintains the ideal distance from the workpiece. The process relies on a height sensor, often mounted on the cutting head, which continuously measures the distance between the torch and the material. This data is then sent to the controller, which adjusts the movement of the z-axis in real-time to maintain the optimal height.
One of the main reasons torch height control is so critical is that the optimal height is directly related to the plasma cutting process itself. Plasma cutting works by blowing a high-velocity jet of ionized gas (plasma) through the material to melt and remove the metal. The gap between the torch and the material significantly affects the shape, accuracy, and smoothness of the cut. If the torch is too close, it can cause excessive molten material to be expelled, leading to poor cut quality. Conversely, if the torch is too far from the material, the plasma arc may become unstable, resulting in a weak or inconsistent cut.
The PoKeys57CNCpro4x25 controller plays a vital role in optimizing torch height control by processing the feedback from the height sensor and making necessary adjustments in real-time. This precise feedback loop ensures that the torch remains at the correct height throughout the entire cut. With the PoKeys57CNCpro4x25 managing these inputs, plasma cutting becomes far more reliable and predictable, allowing operators to focus on other aspects of the process rather than constantly monitoring and adjusting the torch height manually.
In addition to improving cut quality, torch height control also contributes to increased efficiency and reduced wear on both the plasma torch and the workpiece. When the torch is maintained at the correct distance, it minimizes unnecessary heat buildup, which can lead to premature wear of the consumables. It also ensures that the plasma cutter operates at its most efficient level, reducing energy consumption and increasing the overall lifespan of the equipment. This dynamic control also helps when cutting materials of varying thicknesses or when dealing with warped or uneven surfaces, as the THC system compensates for changes in height and material variation.
Moreover, torch height control can be further enhanced when integrated with the CNC controller with drivers. By linking the THC system to the controller, operators can configure the system to respond quickly to changing conditions during the cut. For example, the controller can trigger an automatic height adjustment when the material’s thickness fluctuates or if the torch starts to deviate from the optimal path. This integration ensures that the cutting process remains smooth and consistent, even in challenging conditions.
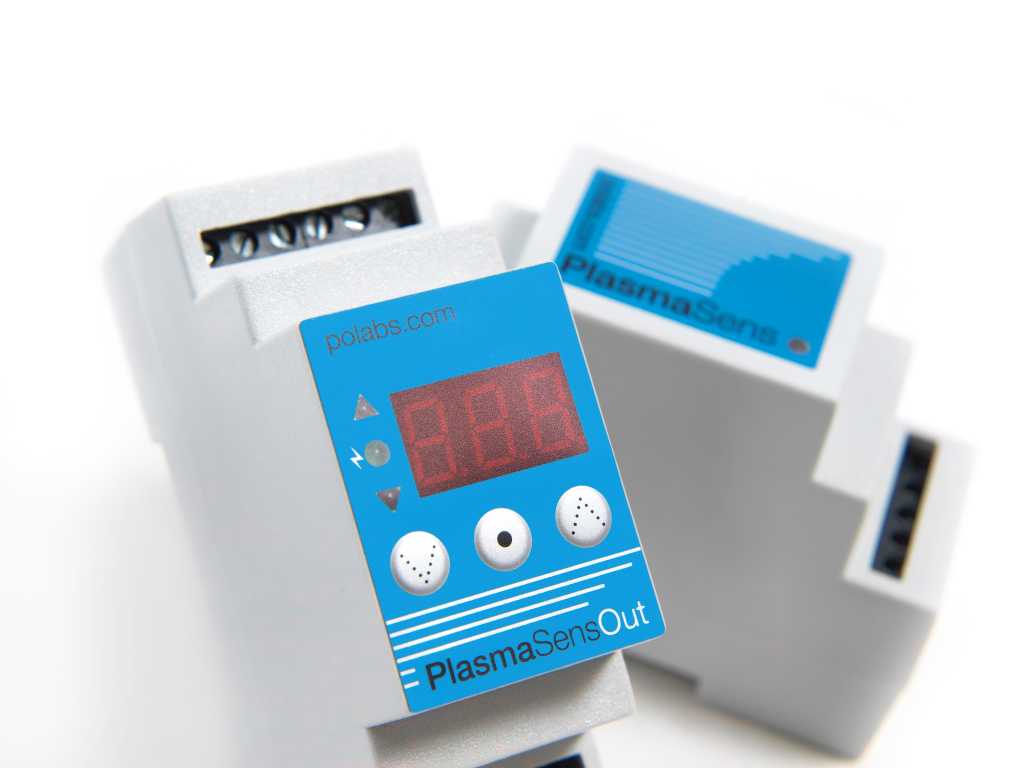
While manual height adjustments are possible, they are not as precise or efficient as automated torch height control. Manual adjustments can be time-consuming and prone to human error, whereas automated systems ensure real-time adjustments without the need for constant oversight. This results in smoother, more accurate cuts, which is especially important for complex designs or high-precision tasks.
In conclusion, torch height control is an indispensable component in a CNC plasma cutting system. It ensures that the plasma torch maintains the optimal height during the cutting process, which directly impacts the quality of the cuts, the longevity of the consumables, and the overall efficiency of the system. Integrated with the PoKeys57CNCpro4x25 and a reliable CNC controller with drivers, torch height control allows for precise, real-time adjustments, eliminating the need for manual intervention and ensuring that every cut is as accurate and high-quality as possible. As we move forward, we will explore how properly setting up the plasma cutter contributes to achieving these results, ensuring the entire system operates at its peak performance.
Plasma Cutter Setup – The Key to Precision and Efficiency
Setting up a plasma cutter properly is a fundamental step in ensuring that your CNC plasma cutting system delivers high-quality results. While the PoKeys57CNCpro4x25 and CNC controller with drivers contribute significantly to the accuracy and control of the system, the plasma cutter setup itself dictates how efficiently the machine performs the actual cutting process. Proper setup influences factors like cut quality, material compatibility, power settings, and overall machine longevity. In this chapter, we will discuss how to set up your plasma cutter correctly to work seamlessly with your CNC system, ensuring optimal performance and precision.
The first step in a successful plasma cutter setup is selecting the appropriate plasma cutter for the job. There are various plasma cutters available in the market, each designed to handle specific materials, thicknesses, and cutting speeds. Choosing the right plasma cutter based on your cutting requirements is crucial. For instance, cutting thin sheet metal will require different settings compared to thicker, tougher materials like steel or aluminum. Understanding the capacity of your plasma cutter and matching it to your materials and project needs ensures that the system operates at its maximum efficiency.
Once the correct plasma cutter has been chosen, the next aspect of the setup involves configuring the power settings. Most plasma cutters allow users to adjust the output amperage, which controls the energy applied to the plasma arc. The PoKeys57CNCpro4x25 and CNC controller with drivers can help fine-tune these settings by coordinating the output between the plasma cutter and the machine’s movements. It’s essential to set the amperage according to the material being cut. Too high of an amperage could lead to excessive material melting and poor cut quality, while too low can result in incomplete cuts or excessive dross buildup. The controller’s integration with the plasma cutter helps automate and optimize these settings based on the material’s thickness and type.
Another critical element in the plasma cutter setup is the torch, specifically ensuring that the consumables are installed correctly. Plasma torches consist of various parts, such as electrodes, nozzles, and swirl rings, all of which wear down over time. It’s vital to regularly inspect and replace these consumables to maintain the cutting performance of the plasma cutter. The PoKeys57CNCpro4x25 and torch height control system work together to ensure that the correct distance is maintained between the torch and the workpiece, preventing unnecessary wear and extending the life of the consumables. This also reduces the chances of misfires or inconsistent cutting, both of which can ruin the quality of the final product.
In addition to the torch itself, it’s important to set up the air supply system properly. Plasma cutters rely on compressed air (or sometimes nitrogen) to generate the plasma arc. The air flow must be consistent, dry, and clean to ensure that the plasma jet is stable and that no contaminants interfere with the cutting process. The air pressure needs to be set according to the plasma cutter’s specifications, typically between 60 and 120 psi, depending on the machine. Maintaining the right air pressure also helps optimize the cutting speed and prevents the plasma cutter from overworking, which could lead to overheating and premature failure.
The PoKeys57CNCpro4x25 and the CNC controller with drivers also play an important role in managing the plasma cutter’s startup and shutdown processes. Ensuring that the plasma cutter is activated and deactivated at the right times during the cutting cycle minimizes unnecessary wear on the equipment and prevents mistakes. For example, the system can be programmed to only fire the plasma when the torch is at the correct position relative to the material, eliminating the risk of accidental cutting or damage to the workpiece. Automated processes like this help streamline workflow and ensure greater reliability throughout the cutting process.
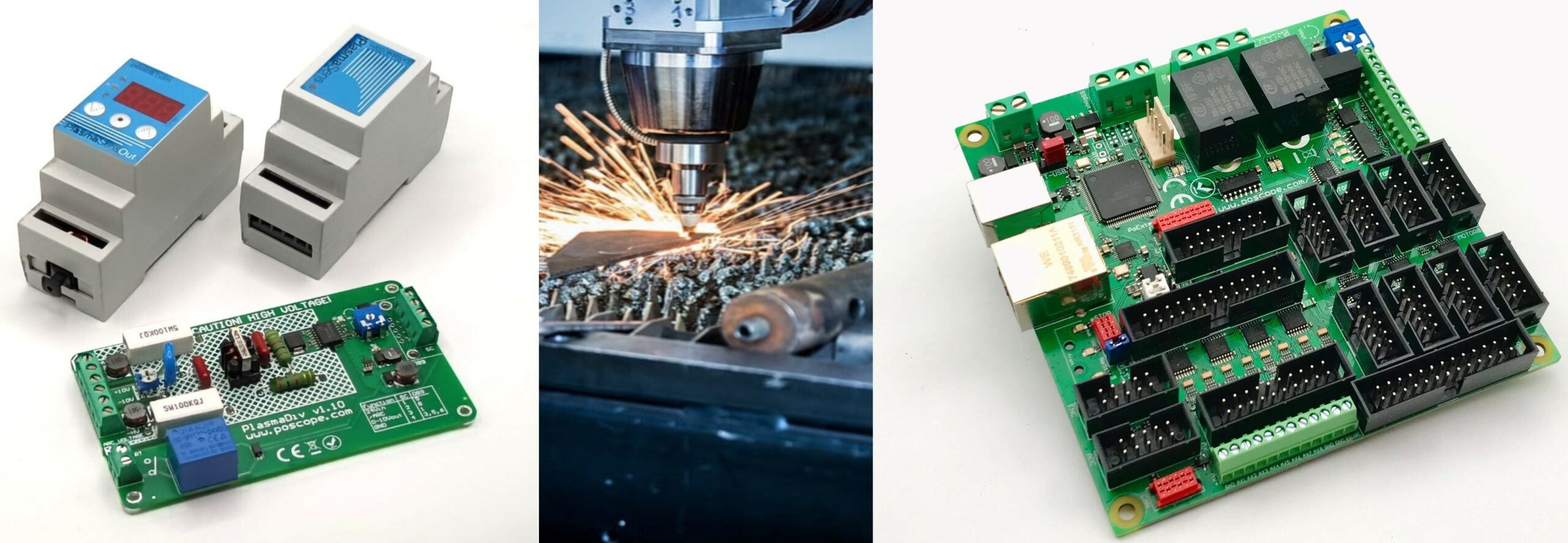
Finally, the plasma cutter setup involves calibration and testing. Before starting any cutting project, it’s essential to perform test cuts on scrap material to check the machine’s settings and adjust as needed. During the test cuts, it’s important to monitor the cut quality, ensuring the edges are clean, the kerf width is appropriate, and there is minimal spatter or dross. Fine-tuning the settings through trial and error, while closely monitoring the results, allows operators to optimize the system for the specific materials and cuts required. The torch height control system can be adjusted to maintain the correct height throughout the test cuts, ensuring that any adjustments to the plasma cutter settings result in the best possible outcome.
In conclusion, the plasma cutter setup is an essential step in ensuring that your CNC plasma cutting system works efficiently and produces high-quality results. Properly choosing the right plasma cutter, setting the correct power parameters, maintaining consumables, and managing air supply are just a few of the critical elements that contribute to success. Integrating the PoKeys57CNCpro4x25 controller with a CNC controller with drivers and a torch height control system enhances the precision and reliability of the entire setup, allowing for seamless operation and superior cut quality. By taking the time to properly configure and maintain your plasma cutter, you can ensure that every job is completed with the utmost accuracy and efficiency, ensuring professional-level results every time.
Conclusion
In CNC plasma cutting, precision and efficiency are paramount, and achieving both requires a comprehensive approach that integrates various critical components. The PoKeys57CNCpro4x25, CNC controller with drivers, torch height control, and plasma cutter setup are all key pieces of the puzzle that work together to ensure smooth, high-quality cuts with minimal downtime. Each element plays a specific role in enhancing the performance of the CNC plasma cutting system, from managing the motion and synchronization of the machine to dynamically adjusting the torch height and optimizing the plasma cutting process itself.
The PoKeys57CNCpro4x25 acts as the central controller, seamlessly coordinating the functions of the system and ensuring that everything from motor movement to feedback loops operates as intended. Its integration with a CNC controller with drivers allows for precise motion control, while its ability to manage additional components like torch height control ensures that the plasma cutter remains at the optimal height for each cut, preventing errors and reducing wear on both the machine and consumables.
Torch height control further enhances the system’s efficiency by ensuring a consistent gap between the plasma torch and the workpiece, critical for achieving clean, precise cuts. By continuously monitoring and adjusting the height during the cutting process, this system reduces the chances of errors related to uneven material thickness or variations in torch positioning. Coupled with a well-set-up plasma cutter, which is calibrated to the specific needs of the material and project at hand, the entire CNC plasma cutting system becomes a powerful tool for achieving accurate, high-quality results with minimal waste or rework.
Ultimately, when all of these components work in harmony, they provide an optimized and reliable CNC plasma cutting system that delivers consistent results, whether you’re cutting intricate designs or large-scale projects. By carefully setting up and fine-tuning your system, you can ensure that it operates at its best, extending the lifespan of your equipment and improving your overall workflow.
In conclusion, whether you’re just starting with CNC plasma cutting or looking to upgrade your existing setup, understanding and integrating the PoKeys57CNCpro4x25, CNC controller with drivers, torch height control, and a precise plasma cutter setup will help you achieve the highest standards of performance and cut quality. With the right equipment and careful attention to detail, you can transform your CNC plasma cutting system into a highly efficient, precision-driven operation, ensuring that every project is completed to perfection.